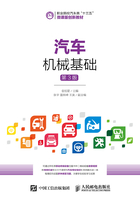
1.3 金属的热处理
金属热处理是将金属工件放在一定的介质中加热到适宜的温度,并在此温度中保持一定时间后,又以不同速度冷却的一种工艺。金属的热处理是在专用的热处理设备上完成的,如图1-12所示。

图1-12 热处理设备
金属热处理是机械制造中的重要工艺之一,与其他加工工艺相比,热处理一般不改变工件的形状和整体的化学成分,而是通过改变工件内部的显微组织,或改变工件表面的化学成分,赋予或改善工件的使用性能。其特点是改善工件的内部质量,而这一般不是肉眼所能看到的。

典型零件的热处理过程
为使金属工件具有所需要的力学性能、物理性能和化学性能,除合理选用材料和各种成形工艺外,热处理工艺往往是必不可少的。钢铁是机械工业中应用最广的材料,钢铁显微组织复杂,可以通过热处理予以控制,所以钢铁的热处理是金属热处理的主要内容。另外,铝、铜、镁、钛等及其合金也都可以通过热处理改变其力学、物理和化学性能,以获得不同的使用性能。
热处理工艺一般包括加热、保温、冷却三个过程,有时只有加热和冷却两个过程。这些过程互相衔接,不可间断。
加热是热处理的重要工序之一。金属热处理的加热方法很多,最早是采用木炭和煤作为热源,进而应用液体和气体燃料。电的应用使加热易于控制,且无环境污染。利用这些热源可以直接加热,也可以通过熔融的盐或金属,以至浮动粒子进行间接加热。
金属加热时,工件暴露在空气中,常常发生氧化、脱碳(即钢铁零件表面碳含量降低),这对于热处理后零件的表面性能有很不利的影响。因而金属通常应在可控气氛或保护气氛中、熔融盐中或真空中加热,也可用涂料或包装方法进行保护加热。
加热温度是热处理工艺的重要工艺参数之一,选择和控制加热温度,是保证热处理质量的主要问题。加热温度随被处理的金属材料和热处理的目的不同而异,但一般都是加热到相变温度以上,以获得高温组织。另外转变需要一定的时间,因此当金属工件表面达到要求的加热温度时,还须在此温度保持一定时间,使内外温度一致,使显微组织转变完全,这段时间称为保温时间。采用高能密度加热和表面热处理时,加热速度极快,一般就没有保温时间,而化学热处理的保温时间往往较长。
冷却也是热处理工艺过程中不可缺少的步骤,冷却方法因工艺不同而不同,主要是控制冷却速度。一般退火的冷却速度最慢,正火的冷却速度较快,淬火的冷却速度更快。
根据热处理目的和工艺方法的不同,热处理一般可分为整体热处理、表面热处理和化学热处理。
① 整体热处理(普通热处理)。如退火、正火、淬火、回火等。
② 表面热处理。如火焰加热表面淬火、感应加热表面淬火和其他表面热处理。
③ 化学热处理。包括渗碳、渗氮、碳氮共渗(氰化)和其他化学热处理。
根据热处理的作用可分为最终热处理和预备热处理。
① 最终热处理。其作用是使钢件得到使用要求的性能,如淬火、回火、表面淬火等。
② 预备热处理。其作用是消除加工(锻、轧、铸、焊等)所造成的某些缺陷,或为以后的切削加工和最终热处理做好准备。例如,钢锻件一般要进行退火或正火,改变锻造后因变形程度不均匀和终锻温度控制不良而造成的晶粒粗大或不均匀现象;调整硬度适合于切削加工,并为以后的淬火做好准备。这种退火或正火,就属于预备热处理。当然,如果零件的性能要求不高,退火或正火后性能已满足使用要求,以后不再进行其他热处理,则退火和正火也属于最终热处理。
1.3.1 整体热处理
1. 退火
根据钢的化学成分和钢件类型的不同,退火工艺可分为完全退火、球化退火和去应力退火等。
(1)完全退火
完全退火又称为重结晶退火,一般简称为退火。完全退火的工艺是将钢件加热到临界温度(临界温度是指固态金属开始发生相变的温度)以上的某一温度,经保温一段时间后,随炉缓慢冷却至500℃~600℃以下,然后在空气中冷却的一种热处理工艺。
完全退火可以达到细化晶粒的目的。在退火的加热和保温过程中,还可以消除加工造成的内应力,而缓慢冷却又可避免产生新的内应力。由于冷却缓慢,能得到接近平衡状态的组织,故钢的硬度较低。完全退火一般适用于中碳钢和低碳钢的锻件、铸钢件,有时也可用于焊接件。
(2)球化退火
球化退火的工艺是将钢件加热至临界温度以下的某一温度,保温足够时间后随炉冷却至600℃,再出炉空冷的退火工艺。
球化退火一般适用于高碳钢的锻件。因此,对工具钢、轴承钢等锻造后必须进行球化退火,避免这些锻件在淬火加热时产生过热、淬火变形和开裂现象,同时能降低锻件硬度,便于切削加工。
(3)去应力退火
去应力退火又称为低温退火。去应力退火一般只需把钢件加热至500℃~650℃,保温足够时间,然后随炉冷却至200~300℃以下后出炉空冷。
去应力退火的目的是消除钢件焊接和冷矫时产生的内应力;消除精密零件切削加工(如粗车、粗刨等)时产生的内应力,使这些零件在以后的加工和使用过程中不易产生变形。
2. 正火
正火是将工件加热至临界温度以上的某一温度,保温一段时间后,从炉中取出在空气中自然冷却的一种热处理工艺。正火的目的与退火相似,主要区别是正火加热温度比退火高,冷却速度比退火快。因此,同样的工件正火后的强度、硬度比退火后的高。
低碳钢件正火可适当提高其硬度,改善切削加工性。对于性能要求不高的零件,正火可作为最终热处理。一些高碳钢件需经正火消除网状渗碳体后,才能进行球化退火。
3. 淬火
淬火是将工件加热到临界温度以上的某一温度,保温一定时间后,然后在水、盐水或油中急剧冷却的一种热处理工艺。淬火的目的是提高钢的硬度和耐磨性。
淬火工艺中淬硬性和淬透性的概念应加以重视和区分:淬硬性是指钢经淬火后能达到的最高硬度。淬硬性主要取决于钢中的含碳质量分数,钢中含碳质量分数高,则淬硬性好。淬透性是指钢在淬火时获得淬硬层深度的能力。淬硬层越深,淬透性越好。淬透性取决于钢的化学成分(含碳质量分数及合金元素含量)和淬火冷却方法,如加入锰、铬、镍、硅等合金元素可提高钢的淬透性。淬硬性和淬透性对钢的力学性能影响很大,因此钢的淬硬性和淬透性是合理选材和确定热处理工艺的两项重要指标。
由于钢在淬火时的冷却速度快,工件会产生较大的内应力,极易引起工件的变形和开裂,因此淬火后的工件一般不能直接使用,必须及时回火。
4. 回火
回火是把淬火后的工件重新加热到临界温度以下的某一温度,保温后再以适当冷却速度冷却到室温的一种热处理工艺。
回火的目的是稳定组织和尺寸,降低脆性,消除内应力,调整硬度,提高韧性,以获得优良的力学性能和使用性能。
回火总是在淬火后进行,通常是热处理的最后工序。淬火钢回火的性能与回火的加热温度有关,强度和硬度一般随回火温度的升高而降低,塑性、韧性则随回火温度的升高而提高。根据回火温度的不同,回火可分为低温回火、中温回火和高温回火。
(1)低温回火
低温回火(加热温度150℃~250℃)主要为了降低淬火内应力和脆性,并保持高硬度;用于处理要求硬度高、耐磨性好的零件,如各种工具(刀具、量具、模具)、滚动轴承等。
为了提高精密零件与量具的尺寸稳定性,可在100℃~150℃以下进行长时间(可达数十小时)的低温回火。这种处理方法称为时效处理或尺寸稳定化处理。
(2)中温回火
中温回火(加热温度350℃~500℃)可显著减小淬火应力,提高淬火件的弹性和强度。中温回火主要用于处理各种弹簧、发条及锻模等。
(3)高温回火
高温回火(加热温度500℃~650℃)可消除淬火应力,使零件获得优良的综合力学性能。通常把淬火后再进行高温回火的热处理方法称为调质。调质广泛用于处理各种重要的、受力复杂的中碳钢零件,如曲轴、丝杠、齿轮、轴等;也可作为某些精密零件,如量具、模具等的预备热处理。
1.3.2 表面热处理
表面热处理是对工件表面进行强化的金属热处理工艺。它不改变零件心部的组织和性能,广泛用于既要求表层具有高的耐磨性、抗疲劳强度和较大的冲击载荷,又要求整体具有良好的塑性和韧性的零件,如曲轴、凸轮轴、传动齿轮等。表面热处理可分为表面淬火和化学热处理两大类。
1. 表面淬火
表面淬火是利用快速加热的方法,将工件表层迅速升温至淬火温度,不等热量传至心部,立即予以冷却,使得表层淬硬,以获得高硬度和耐磨性,而内部仍保持原来组织,从而具有良好的塑性和韧性。这种热处理工艺适用于要求外硬(耐磨)内韧的机械零件,如凸轮、齿轮、曲轴和花键轴等。零件在表面淬火前,须进行正火或调质处理,表面淬火后要进行低温回火。

钢的表面淬火原理
按表面加热的方法,表面淬火可分为感应加热表面淬火、火焰加热表面淬火和电接触加热表面淬火等。由于感应加热速度快、生产效率高,产品质量好,易实现机械化和自动化,因此感应加热表面淬火应用最为广泛,但设备较贵,主要用于大批量生产。
根据感应电流频率不同,感应加热表面淬火又分为高频、中频和工频淬火。
2. 化学热处理
化学热处理是将钢件放在某种化学介质中,通过加热和保温,使介质中的一种或几种元素渗入到钢的表层,以改变表层的化学成分、组织和性能的热处理工艺。
化学热处理的种类很多,一般都以渗入元素来命名。表面渗层的性能取决于渗入元素与基体金属所形成合金的性质及渗层的组织结构。常见的化学热处理有渗碳、氮化、碳氮共渗、渗金属(如渗铬、渗铝等)和多元共渗等。渗碳、氮化、碳氮共渗用来提高工件表层的硬度与耐磨性;渗铬、渗铝能使工件表层获得某些特殊的物理、化学性能,如抗氧化性、耐高温性、耐蚀性等。

钢的化学热处理原理
【例1-1】 某型号柴油机的凸轮轴,要求凸轮表面有高的硬度(HRC>50),而心部具有良好的韧性,原采用45钢调质处理再将凸轮表面进行高频淬火,最后低温回火,现因库存不足,拟用15钢代替。试说明:
(1)原45钢各热处理工序的作用。
(2)改用15钢后,按原热处理工序进行能否满足性能要求?为什么?
(3)改用15钢后,为达到所要求的性能,在心部强度足够的前提下采用何种热处理工艺?
解 (1)调质处理可获得高的综合机械性能和疲劳强度;局部表面淬火及低温回火可获得局部高硬度和耐磨性。
(2)不能。改用15钢后按原热处理工序会造成心部较软,表面硬,并造成表面脱落。
(3)可采用渗碳处理。
【例1-2】 根据汽车发动机的工作特点,参照图5-1,试阐述活塞、曲轴、排气阀、气门弹簧及轴承等零部件的材料及热处理工艺的选择策略。
解 (1)活塞是发动机曲柄连杆机构中在燃烧室内上下往复运动的零件。它的主要功能是密封燃烧室,上下运动压缩燃料气体和承受并传递燃料爆燃膨胀力到曲轴。所以在工作中它的顶面受到周期变化的气体压力,它与连杆连接的活塞销座受到机构惯性力、扭转、冲击力等,它的侧壁的密封环槽受到循环应力等。因比对活塞的性能要求是:质量轻、耐热、耐蚀、气密性好、强度高、冲击韧性较好、扭转疲劳强度较好。从质量轻、耐热、耐蚀性能考虑选择铝合金;从气密性好和机械性能较高方面考虑,以强度、韧性为设计指标,考虑疲劳强度,选择变形硬铝合金LD7为宜。
(2)曲轴是发动机曲柄连杆机构中旋转轴零件。它的功能是将活塞传递的气体压力通过连杆转换为旋转机械能。所以它要受到周期变化的拉压应力、旋转惯性力、扭转、弯曲应力、冲击力以及高速运动的扭转振动力作用。因此曲轴的性能要求是:高强度、良好的冲击韧性、弯曲和疲劳强度,还要考虑轴颈处的高硬度和耐磨性。根据发动机功率和转速决定的曲轴工况应力确定强度、塑性和冲击韧性为设计指标,考虑疲劳强度、耐磨性和经济性,小功率低转速时选择高强球铁为宜,中高功率和转速时选择中碳调质钢为宜。
(3)排气阀是发动机燃烧室排放燃烧完废气的阀门。它在工作时要经受高温废气的压力,不排气时要保证密封不泄漏气体。长期高温环境下使用需有足够的高温强度、持久强度、抗蠕变、良好的热疲劳强度、韧性和抗氧化性。同时它的组织在高温工作环境下要稳定,不能发生再结晶变化,保证材料高温机械性能不恶化。所以选择热强钢材料为宜,考虑发动机排气阀工作温度约600℃,高温性能设计指标等,选用马氏体热强钢,如4Cr9Si2钢等。
(4)气门弹簧是发动机燃烧室外压紧气门的弹簧零件。在进气或排气时凸轮挺杆的张力大于弹簧力,弹簧弹性变形打开气门,随后外张力减小至消失,弹簧弹性收缩又压紧气门,如此不断周期循环工作。因此它的性能要求是:满足控制气门开启和关闭的弹性极限,较高的疲劳极限和缺口疲劳极限,足够的塑性、韧性,良好的表面质量,较好的淬透性,低的脱碳敏感性等。所以选择弹簧钢,进一步考虑强度设计和结构设计性能指标和较小几何尺寸,选择60Mn或65Mn即可。
(5)滑动轴承是支撑发动机内运动件并保证其正常运动的零件。它在工作时不仅承受轴的压力,而且与轴颈之间有相对滑动,产生摩擦磨损。为保证轴的磨损最小、并满足轴承工作条件,滑动轴承的性能要求是:在工作温度下有足够抗压强度、疲劳强度、塑性和韧性,与轴的摩擦系数最小并能贮存润滑油、具有良好磨合能力、抗蚀性、导热性和较小膨胀系数,良好工艺加工性和经济性。考虑以上要求,选择轴承合金。根据发动机功率和转速确定的滑动轴承强度指标、工作温度、耐磨性等实际参数,确定具体轴承合金和牌号。通常大型重载低速发动机选择锡基轴承合金,中低载低速发动机选择铅基轴承合金,高速高压发动机选择铜基轴承合金。