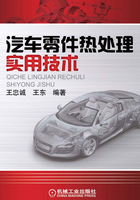
2.2活塞连杆机构的热处理
2.2.1活塞
1.工作条件和性能要求
活塞为曲柄连杆机构的主要部件,活塞的功能是与气缸盖、气缸壁共同组成燃烧室,承受气缸中气体的压力并通过活塞销和连杆传给曲轴。
活塞在工作过程中受力比较复杂:活塞交替地压向气缸壁,侧向压力作用于活塞裙部;活塞裙、活塞环槽和活塞销孔凸部都受到摩擦力的作用;混合气的燃烧使气缸内产生2500K以上的高温,通过活塞顶、活塞环带和活塞环将大量的热传给气缸壁。可见,活塞承受不同类型的应力与应变,故应具有低的密度、足够的强度与刚度、良好的耐热性、优异的传热性、摩擦力小以及良好的耐磨性、温度变化时尺寸及形状变化小等特性,满足其服役需要。引起活塞损坏的原因包括发动机装配和安装操作不当(如气缸盖螺栓拧紧不均匀引起的气缸变形、活塞销在连杆孔中装配过紧、气缸套不规则等)。常见的失效方式为活塞拉伤(无油运行拉伤)、活塞顶穿孔、烧蚀、变形与断裂等。
2.活塞材料的选用
为满足活塞的以上技术要求,发动机广泛采用的活塞材料是铸造铝合金,常采用ZL108、ZL109、ZL110、ZL201等,它们具有较高的高温强度和低膨胀系数,适于制作发动机活塞、气缸头以及高温零件。有的柴油机也采用高级铸铁或耐热钢制造活塞。另外可采用铝硅合金(AlSi12CuNi)制造活塞,更高负荷则采用AlSi18CuNi、AlSi25CuNi制造活塞。铝合金活塞具有导热性好、质量轻、易于加工等特点,均是铸造加工的,应用比较广泛。
3.活塞的热处理
(1)活塞的技术要求 铸造铝合金经过热处理后,同一活塞中的硬度差应不大于10HBW,其力学性能与体积稳定性见表2-1。金相组织应符合JB/T 6289—2005《内燃机 铸造铝活塞 金相检验》的规定。
表2-1活塞的力学性能与体积稳定性
注:其中D为活塞的直径。
(2)活塞的热处理工艺 活塞常用铸造铝合金的热处理工艺规范见表2-2。
表2-2活塞常用铸造铝合金的热处理工艺规范
(3)表面处理 表面处理包括镀铬、喷钼、镀锡以及渗氮等。
4.活塞的热处理操作与质量检验
1)活塞采用吊装或装夹具加热,铸件要均匀分层摆放,避免叠压,在加热温度下装炉,不要接触炉壁。
2)固溶加热设备的控温精度不大于±5℃,时效处理控温精度应不大于±10℃,否则会造成活塞硬度与体积稳定性不符合要求。
3)固溶处理的转移时间应不超过15~20s,活塞淬入水中要不停运动,在水中的冷却时间不少于5min,并立即在油中或硝盐中进行时效处理。
4)活塞的热处理质量检验包括硬度、抗拉强度等,在本体上取样进行性能检测。
5.铝合金活塞的热处理缺陷分析与对策(表2-3)
表2-3铝合金活塞的热处理缺陷分析与对策
2.2.2活塞环
1.工作条件和性能要求
活塞环是汽车发动机中的重要零件,它对发动机的功率、油耗以及缸体寿命有较大的影响。活塞环包括气环和油环,气环用来密封气体,即用来封闭活塞与气缸之间的间隙,防止气缸漏气和高温下燃气滴入曲轴箱内,同时将活塞上的热量传给冷却的气缸,帮助活塞散热。油环安装在活塞的油环槽内,油环的作用是把缸壁上的机油刮布均匀和将多余的机油收集在槽内,并经槽底通孔流回油底壳,减少缸壁上的机油刮入燃烧室内造成燃烧室积炭,避免机油的消耗量增大。
要求活塞环具有足够高的弹性极限,良好的耐磨性及一定的抗擦伤性,一定的强度、韧性、抗疲劳性,良好的导热性和良好的抗燃气腐蚀性。其主要的失效形式为擦伤、磨损和疲劳折断。
2.材料的选用
根据活塞环的功能与工作条件,制造活塞环的材料应具有良好的耐磨性、储油性、导热性、耐热性和高的冲击韧度,弹性与弹性模量大,具有足够的强度(包括抗折强度与疲劳强度)等。活塞环通常采用高强度优质灰铸铁、合金铸铁、可锻铸铁等制造,上压缩环用合金铸铁,其余高应力活塞环是由球墨铸铁或高合金钢制造的。
球墨铸铁作为活塞环的材料,应用最为广泛。对于强力发动机,为保持其动能而采用高合金铸铁,如Cu-V-Ti合金铸铁、Cr-Mo合金铸铁、高P铸铁、W-V-Ti铸铁及球墨铸铁等。这些材料普遍具有高的耐磨性和耐蚀性,在活塞的反复运动过程中,始终能确保不漏油和气,同时也易于制作,具有小的摩擦因数。活塞环的形式如图2-1所示,第一道气环和第二道气环是防止燃烧气体泄漏的密封环,而油环的主要作用是控制润滑气缸内壁和活塞的润滑油的油量。
通常钢制活塞环选用的材料为65Mn、50CrVA、T8A、20Cr13、95Cr18等。钢制作的活塞环具有强度高、抗折断、成本低等优点,钢带组合油环的控油效果好。
图2-1 活塞环
目前国外已经开始采用铁基粉末冶金材料制造活塞环,它具有金属利用率高、材料性能好、内部空隙储油功能,具有良好的发展前景。
3.活塞环的热处理
考虑到活塞环粗加工后加工应力较大,要进行去应力退火处理。铸铁的石墨形状为片状,具有良好的导热性、耐磨性和抗擦伤能力,加入合金元素后提高了热稳定性,细化了晶粒和提高了耐磨性,因此合金铸铁广泛应用于制作活塞环。
活塞环的热处理技术要求为硬度98~108HRB,同一活塞环上硬度差不大于3HRB;其组织为细片珠光体(或索氏体)+体积分数少于20%的石墨(长度为0.12~0.18mm)+体积分数少于5%的铁素体(应分散分布)+磷共晶碳化物(应呈细小均匀分布)。
(1)去应力退火 温度在550~570℃范围内,保温120min结束后出炉空冷或炉冷至480℃出炉空冷,可将加工应力消除90%以上。后一种处理的活塞环的硬度均匀性好。通常铸铁环在粗磨两端面后退火,目的是消除铸造和机械加工应力、稳定尺寸和精度等。
(2)活塞环的热定型(固定) 将缝隙大小固定,以使其压紧于气缸壁内,在工作过程中有适当的弹性。热定型是去应力退火的一种形式,活塞环的热定型采用专用夹具,上下为两个压盘,中间穿螺栓压紧,其中一个底盘固定。定型杆的宽度等于活塞环(胀圈)定型后的开口尺寸。压紧的程度以装好后用力抖动活塞环的位置不变为宜。装夹后的活塞环可在可控气氛炉中加热,温度的选择以不破坏铸铁的组织为原则。定型处理后的硬度为220~270HBW(98~105HRB)。具体铸铁活塞环热定型工艺规范如图2-2所示。
定型后的活塞环改善了组织,降低了基体的硬度,消除了应力,获得了一定的残留变形。为了保持弹性的稳定,活塞环还要在气缸中进行400℃、保温2~4h的稳定化处理。
铸铁活塞环调质处理的目的是提高弹性模量与热稳定性,球墨铸铁活塞环调质处理的工艺规范如图2-3所示。
图2-2 铸铁活塞环热定型工艺规范
图2-3 球墨铸铁活塞环调质处理的工艺规范
(3)钢带活塞环的热处理 钢带活塞环的热处理工艺规范如图2-4所示。
(4)活塞环的表面处理 其目的是为了提高活塞环的表面硬度与耐磨性,改善表面的储油能力,以防粘着磨损,改善与气缸壁的磨合性能,提高其耐热性;加快活塞环的初期磨合,以改善活塞环与气缸的运动条件。
图2-4 钢带活塞环的热处理工艺规范
1)一般气环的工作条件差,外圆面上要进行多孔性镀铬,具有硬度高、可储存少量的润滑油、使用寿命提高2~3倍等特点。另外,也可喷涂钼或进行渗氮、激光热处理,端面进行磷化处理同样可起到良好的作用。
2)油环镀锡或磷化处理,也可镀铬或喷涂钼,改善磨合性能和提高活塞环的耐磨性。压缩环镀铬层深度≥0.10mm,油环镀铬层深度≥0.08mm。镀铬后的活塞环要进行去氢处理,镀铬层硬度不低于750HV(200HRB)。应对活塞环的未磨损部位进行防蚀处理,常见的方法为镀锡、渗氮等,渗层深度为0.001~0.003mm。
表2-4列出了常见铸铁活塞环的性能对比。
表2-4常见铸铁活塞环的性能对比
活塞环的表面处理在其制造过程中占有十分重要的地位,在生产中大量采用了上述处理工艺方法,提高了活塞环的耐磨性。对要求更高的耐热性和抗粘着活塞环,可进行喷涂钼处理,为便于比较几种表面处理工艺及性能,将其列于表2-5中供参考。
表2-5活塞环表面处理工艺及其性能特点
活塞环镀铬后的硬度比热处理后的硬度约高2.5倍,其耐磨性提高,电解析出的铬层与基体金属具有较高的结合强度,同时镀铬温度在70℃以下,故不会破坏活塞环原来的金相组织,也不会使活塞环产生热应力变形,故其应用十分广泛。
活塞环除了采用镀铬与喷涂钼处理外,其他的表面处理还包括磷化处理与发蓝处理,少数采用渗硫或渗氮处理。磷化处理是以加快活塞环初期磨损、防止擦伤气缸为主要目的表面处理方法,在90~98℃的温度下进行,蒸汽磷化法的磷化时间可缩短到普通的1/10。
(5)钢带活塞环的热处理与表面处理 常用的钢带活塞环材料为50CrVA、65Mn、T8A等,刮环用钢带的热处理是在管式可控气氛炉中进行的,淬火冷却介质为机械油。热处理后的钢带在绕圈机上缠绕后,与定型胎套一起放进热定型筒中密封,在电阻炉中进行定型处理。具体热处理工艺规范见表2-6。
表2-6常用钢带活塞环材料的淬火和回火、定型热处理工艺规范
国外钢制活塞环通常选用Cr13、Cr18等高碳高铬马氏体不锈钢制作,在调质处理后进行氮碳共渗处理(560~580℃×2~3h),渗氮层深度在0.05mm以上,目的是提高活塞环的耐磨性与抗咬合性,进行表面强化处理,但需要采用活塞环专用渗氮工艺装备,防止缩口,以确保自由开口与尺寸稳定。
4.活塞环的热处理工艺分析与操作要点
1)活塞环的热定型包括铸铁热定型与钢带热定型两种,前者采用盐浴炉或电炉进行处理,后者则在电炉中完成。活塞环在心轴上的装配应压紧,垫片与插入的开口定型金属镶块应垂直无变形。加热完毕后空冷即可。
2)应根据活塞环的磨损与润滑条件采用不同的表面处理方法。为提高活塞环的耐磨性,同时降低气缸的磨损,可选用镀铬工艺。为防止干摩擦,提高缸的抗拉能力,则选择喷钼和镶嵌金属氧化物填料的方法。为使环与气缸突出部位相接触而加剧磨损,缩短磨合期,使活塞环进入稳定的工作状态,应选择镀锡、发蓝和磷化处理等。
3)活塞环作为有特殊要求的零件,在镀铬后应进行除氢热处理,目的是使大部分残留氢气排出,减小零件的脆性,提高其疲劳强度。采用的方法有水煮法(煮沸6h)、油煮法(250℃×2h)和空气加热法(180~200℃×2~3h),其中油煮法效果最好,采用空气加热工艺较为普遍。
4)钢带活塞环的热处理回火温度与定型温度是一致的,硬度不会降低,其回火托氏体组织又具有良好的弹性,起到稳定化的作用。质量检验包括以下内容。
①硬度为98~108HRB,同一活塞环上的硬度差不大于3HRB。
②金相组织为细片珠光体(或索氏体)+体积分数为20%的石墨+体积分数为5%的铁素体(应均匀分布)+磷共晶碳化物(细小均布)。
③外观检查包括:不允许有裂纹、毛刺、锈迹和崩缺等,镀铬后的活塞环表面无铬瘤、铬层裂纹、尖锐铬边和崩块等,铬层与活塞环应牢牢结合,无脱落现象;活塞环外圆表面及上下端面无粗加工后的刀痕、振纹以及氧化皮等,退磁彻底,否则将造成活塞环的异常磨损。
2.2.3活塞销
1.工作条件和性能要求
活塞销是发动机上用于连接活塞和连杆小头的结构件,相当于双点支承架,为钢制的空心圆柱体。其作用是连接活塞和连杆,将活塞承受的气体作用力传递给连杆。由于在较高的温度下工作,同时要承受非对称交变的载荷、一定的冲击力和摩擦力的作用,且表面处于润滑条件较差的摩擦条件下(一般靠飞溅润滑),因此要求它具有足够高的强度和刚度,韧性、表面耐磨性好,具有高的疲劳强度,质量尽可能小,同时要求配合表面有很高的表面质量和尺寸精度等。活塞销失效的主要形式为表面磨损和疲劳裂纹,活塞销的内孔形式如图2-5所示。
2.材料的选用
根据活塞销的工作特点,活塞销在高温下承受极大的周期性冲击载荷,润滑条件差,故要求选用的材料有足够的强度、韧性、耐磨性及高的疲劳极限等,为减小往复惯性力,要求其质量轻。因此,制作活塞销的材料通常选用韧性较好的低碳钢或低合金结构钢(渗碳钢),常见的材料为15、20、12CrNi3A、15Cr、18Cr2Ni4WA、20Cr、20Mn2、20CrMnTi、20CrMnMo等低碳钢与低碳合金结构钢,也采用渗氮钢制造。为提高其在弯曲疲劳下的表面压力,外表面必须进行硬化处理,而内部具有高韧性,事实证明冷拔材料的耐久性较好。
图2-5 活塞销的内孔形式
a)圆柱形 b)组合形 c)两段截柱形
3.活塞销的热处理
(1)技术要求 活塞销的外圆硬度为58~64HRC,其余技术要求见表2-7和表2-8。
表2-7活塞销的心部硬度与壁厚的关系
表2-8活塞销的渗碳技术要求(成品)
活塞销的渗碳层深度较深为0.8~1.9mm时,渗层深度包括共析层深度、过共析层深度和1/2过渡层深度,不允许有大块的碳化物。内孔表面脱碳或贫碳层不大于0.03mm。
(2)退火处理工艺 大多数的活塞销是经冷挤压或温挤压加工成形的,因此热处理前首先进行预备热处理即退火与软化退火。常见活塞销(冷挤压坯料)的退火工艺规范见表2-9。
表2-9常见活塞销(冷挤压坯料)的退火工艺规范
活塞经过挤压成形,材料的晶粒被挤压后出现加工硬化,故应进行软化退火或再结晶退火,其规范为680~720℃×12~14h,炉冷至300℃出炉后空冷。
(3)活塞销的渗碳工艺 一般活塞销采用20Cr、20CrMo经冷挤压成形及进行双面渗碳处理,20Cr钢活塞销渗碳工艺规范见表2-10。
表2-1020Cr钢活塞销渗碳工艺规范
注:此表是在RJJ-90-9渗碳炉中渗碳时的具体数值。
为控制渗碳层碳化物级别,要严格控制碳势。推荐采用双面渗碳,双面渗碳后活塞销内孔表面得到强化,产生了较大的残留压应力,防止了内孔的纵向开裂,同时可抵消部分外加拉应力的作用,因此提高了疲劳强度,延长了其使用寿命。20Cr钢活塞销的渗碳处理工艺为920~940℃×6~10h,具体工艺如图2-6所示。
20钢渗碳层的检验一般是在850℃保温20min空冷后进行的;15Cr、20Cr、20Mn2等经过850℃×15~20min+650℃×10~20min退火后在100倍显微镜下测量。
图2-6 20Cr钢活塞销的具体渗碳工艺规范
(4)淬火和回火 活塞销渗碳结束后既可在860℃左右冷却,也可缓冷到室温后重新在盐浴炉或保护气氛炉中加热处理,在860~870℃保温后油冷。加热保温系数按0.7~0.8δ(单位为min/mm)计算,其中δ为活塞销的壁厚。淬火后的硬度不小于58HRC,应无淬火软点或软带。在硝盐炉或油炉中进行180~200℃×1.5~2h回火处理,回火后硬度控制在58~64HRC,同一活塞销中硬度差不大于3HRC。如采用网带炉或振底炉,则工艺参数为840~850℃×60min,采用循环油冷却,马氏体级别1~5时为合格,碳化物为1~3级时合格。
4.热处理工艺分析与操作要点
1)15Cr钢活塞销930℃渗碳空冷后,采用850℃×2h油冷热处理,要求低温回火后硬度为57~65HRC,抗拉强度为800~1250MPa,但油冷后个别活塞销存在软点,硬度为50~55HRC,抗拉强度明显低于要求。15Cr钢活塞销930℃渗碳后经不同热处理后的各项技术指标的对比见表2-11。
表2-1115Cr钢活塞销930℃渗碳后经不同热处理后的各项技术指标的对比
从表2-11中可知,活塞销油冷后出现软点,心部有铁素体组织,将影响其使用性能。采用三硝水作为淬火冷却介质,则心部形成马氏体组织,抗拉强度在800~1250MPa范围内,完全符合技术要求。
2)15Cr、20Cr钢活塞销渗碳后大多采用二次淬火工艺,其缺点在于渗碳层的碳质量分数为1.0%~1.3%,超过了共析成分,在淬火时得到了较多的碳化物,同时残留奥氏体增加,个别位置的硬度降低,因此在活塞销的摩擦部位会有麻点产生,造成其耐磨性的下降。经反复实践证明,通过调整活塞销的渗碳气氛,控制碳质量分数在0.8%左右,淬火后得到马氏体+均匀分布的颗粒状碳化物,因此可在渗碳后进行一次淬火工艺,20Cr钢活塞销渗碳新工艺如图2-7所示。
图2-7 20Cr钢活塞销渗碳新工艺
3)活塞销除了采用一般的热处理工艺进行淬火和回火外,对其进行高频感应淬火更有意义。高频感应淬火后的显微组织分级是控制产品质量的一个重要指标,活塞销同样也不例外。通常活塞销的显微级别为3~6级,同时3~6级也是高频感应淬火的常见金相组织级别,能满足零件的技术要求和确保零件使用寿命的提高。
感应加热速度快,组织变化比较大,因此显微组织能够及时反映感应淬火后是否过热或欠热、加热不足等,从上面的讲述中可以了解到:3级为中等针状马氏体;4~5级为细针状马氏体;6级为细针状马氏体,是最理想的组织。
4)质量检查检验包括以下几个方面:渗碳层深度符合要求;活塞销的内孔硬度合格,同一销的工作面硬度差不大于3HRC;金相组织为细针状马氏体,允许存在少许粒状碳化物;表面不允许有任何形式的裂纹和锈迹,无尖角、毛刺和氧化物,应进行磁粉无损检测;外圆不得有麻点、黑斑、刻痕以及磕碰伤。
5.活塞销的常见热处理缺陷和预防挽救措施
在活塞销渗碳和热处理过程中,有一些因素直接影响产品质量。常见的活塞销热处理缺陷和预防补救措施见表2-12。另外,材料本身的原因也会造成活塞销的淬火开裂,如材料的化学成分、材料的质量状态及原始应力状态等,而成分主要取决于零件的工作状况和服役条件,高的硬度要选择含碳量高的材料;对于大转矩、大弯矩作用下工作的零件,要求材料具有高的抗扭强度或抗弯强度和高的弯曲疲劳强度等。
表2-12常见的活塞销热处理缺陷和预防补救措施
2.2.4活塞杆
1.工作条件和技术要求
活塞杆同活塞一起在腐蚀的环境下工作,负责动力的传递,在工作过程中受到往复拉、压交变应力的周期作用,活塞环与填料之间发生滑动摩擦,因此要求活塞杆具有足够的强度和高的表面硬度,以及具有抗腐蚀、抗疲劳、抗擦伤和抗咬合能力。
从活塞杆在工作过程中的受力状况而言,选用的材料应为调质钢,热处理后表面硬度高,而内部有良好的综合力学性能。为提高活塞杆的使用寿命,其表面应进行强化处理,以满足其表面耐磨、耐蚀、摩擦因数小的技术要求。
2.材料的选用
38CrMoAlA是活塞杆的首选材料。
3.活塞杆的热处理工艺
热处理技术要求:调质处理硬度为28~35HRC,渗氮层深度大于0.35mm,表面硬度为1100HV5以上,脆性2级,无网状与脉状组织。
(1)材料的预备热处理 38CrMoAlA钢的预备热处理包括正火和调质,其正火工艺为770℃×60min+940℃×30min,保温结束后取出空冷。
调质工艺为880~900℃×30min+930~950℃×25~30min,预冷至880℃左右淬油,在610~630℃×120~180min高温回火后空冷,基体硬度为28~35HRC。
活塞杆经真空热处理可以发挥材料的潜力,避免零件表面的氧化和脱碳,具有表面光亮和变形小等特点,表面的状态没有受到影响,因此明显提高了疲劳强度。
(2)材料的最终热处理——离子渗氮 采用离子渗氮是为了提高活塞杆的表面硬度、获得良好的耐磨性和耐蚀性,可明显提高其使用寿命。
在活塞杆的实际生产过程中通常选用三段离子渗氮工艺,即510~530℃×4h+560~580℃×8h+510~530℃×4h,渗氮结束后随炉降温至100℃以下出炉空冷。渗层深度为0.37~0.39mm,硬度为1096~1150HV5,脆性小于2级,渗氮层无网状、脉状渗氮物,组织正常。
目前用中频感应淬火来代替活塞杆的离子渗氮,实际使用效果不错。首先进行调质处理后再进行中频感应淬火,可使表面硬度控制在52~60HRC之间,变形量小于0.5mm。
4.热处理工艺分析与操作要点
1)正火时活塞杆均匀散开,防止冷却不均匀而影响后面工序的调质处理质量,同时也会产生较大的变形。
2)离子渗氮前的去应力退火温度为580~600℃,保温8~10h。目的是消除校直和机械加工产生的应力或锤击力,避免后面工序中出现变形等缺陷影响加工质量,不能进行人工校直。
3)进行离子渗氮时应对螺纹部分进行保护处理,可套上螺母或铜环等加以屏蔽。
4)质量检验包括基体硬度、组织、表面硬度与渗氮层深度、变形量等,按要求进行检查。
5.活塞杆的常见热处理缺陷与对策(表2-13)
表2-13活塞杆的常见热处理缺陷与对策
2.2.5连杆
1.工作条件和技术要求
汽车发动机连杆(图2-8)将活塞和曲轴连接起来,小头与活塞一起作往复运动,把作用于活塞顶部端面的膨胀气体压力传递给曲轴,将活塞的往复直线运动变为曲轴的旋转运动,连杆在工作过程中将活塞受到的气体压力传递给曲轴,再由曲轴转变成输出的转矩。连杆的大头和曲轴一起作旋转运动,而杆身作十分复杂的平面摆动等,因此连杆在工作过程中会受到交变的拉应力和弯应力作用,同时承受急剧变化的动载荷的冲击,其受力方式十分复杂,整个截面都要承受均匀的拉应力、压应力以及脉动交变应力的作用。因此要求其所用材料具有良好的综合力学性能。
综上所述,连杆在工作过程中受到压缩、拉伸、弯曲和冲击交变载荷作用。因此,和活塞一样,要求连杆质量轻,具有足够的刚度和强度、高的疲劳强度和冲击韧度等,否则连杆螺栓、杆身的大端盖将发生断裂,造成发动机的损坏。作为发动机容易损坏的零件,其损坏形式为断裂,疲劳断裂发生在连杆的三个高应力作用区,即大头与杆身和小头与杆身的过渡区(在螺栓孔附近)以及杆身中间。断裂与原材料缺陷、锻造折叠及淬火裂纹等造成的失效有关。
图2-8 汽车发动机连杆
1—衬套 2—小头 3—杆身 4—螺栓 5—大头 6—轴瓦 7—轴承盖 8、9—止口
2.材料的选用
根据连杆的工作条件和技术要求,连杆调质处理后的显微组织应为均匀、细小的索氏体,为确保连杆既具有足够的强度,又获得较高的韧性以及优良的抗疲劳性能,不得有片状铁素体和非金属夹杂物。最后需进行强化喷丸处理。对于非调质钢可采用铁素体-珠光体钢制造汽车曲轴和连杆工艺,如35VS、35MnV、35MnVS、40MnV以及43MnS等。目前国外汽车公司在赛车上使用钛合金连杆,具有强度更高和质量更轻的特点,减轻了质量且提高了使用寿命。
根据连杆的工作环境的具体要求,连杆通常采用中碳钢或合金钢模锻或辊锻而成,常见的材料有40、45、50、45Mn2、40Cr、35CrMo、42CrMo等,也有少数采用稀土-镁球墨铸铁制造的连杆。
3.连杆的热处理
目前连杆的生产厂家利用锻造余热进行淬火和回火,以此来取代调质工艺,但应注意回火后的连杆在热校直后,仍要进行低温回火处理。
连杆的热处理技术要求为:花键与杆部硬度为37~44HRC,盘外圆硬度为24~34HRC。常见连杆常用材料的预备热处理技术要求见表2-14。
表2-14连杆常用材料的预备热处理技术要求
(1)调质处理 连杆经调质处理后可获得良好的力学性能,降低了硬度,改善了切削加工性,细化了晶粒,为最终热处理做好了组织准备。表2-15为常见碳素钢、合金结构钢连杆调质处理工艺规范。
表2-15常见碳素钢、合金结构钢连杆调质处理工艺规范
(续)
(2)利用锻造余热进行连杆的淬火和回火 该工艺具有可简化程序、节省能源、改善切削加工性、提高力学性能的优点。资料介绍,40Cr和45钢连杆分别利用余热淬火和回火,与调质处理的力学性能相比,抗拉强度、断面收缩率、冲击韧度和硬度均有提高,二者的工艺和力学性能比较见表2-16。一般碳的质量分数为0.40%~0.55%的中碳钢锻件均可采用余热淬火。
表2-1640Cr和45钢连杆锻造余热淬火工艺与一般调质处理的工艺和力学性能比较
(3)连杆的喷丸强化处理 连杆经调质处理后,硬度为228~269HBW,连杆经过喷丸处理后,表层会产生一定的塑性变形,这将使晶体的点阵发生畸变,表层形成高密度的位错缠结,从而使表层得到了强化。采用喷丸强化处理后,连杆表面的残留压应力增大,表面硬度得到了明显提高,如45钢的压应力增大到-350MPa时,其疲劳寿命从48万次提高到190万次以上,即使用寿命约提高到原来的4倍。可见对连杆进行喷丸强化后,明显提高了疲劳强度、使用寿命、抗弯强度等。表2-17为常见连杆材料喷丸强化工艺参数。另外对连杆进行滚压加工也不失为一种良好的强化工艺措施,既可消除切削加工的痕迹,又可使槽的几何尺寸和形状精确,提高了连杆的疲劳寿命。
表2-17常见连杆材料喷丸强化工艺参数
注:0.18C表示C型标准试样的测量弧高为0.18mm。
4.热处理工艺分析与操作要点
1)连杆的锻造加热温度控制在1100~1220℃为宜,终锻温度(淬火温度)为900~1000℃,锻造后油冷应控制入油的停留时间,以防析出铁素体。
2)要控制淬火油温和在油中的冷却时间,连杆要及时回火,否则会引起裂纹的产生。
3)目前,对连杆进行中频感应加热是一种经济有效的毛坯热处理方法,处理后的各项技术指标符合连杆的要求。
4)40、40Cr、40MnB钢连杆的热处理质量检验项目见表2-18。
表2-1840、40Cr、40MnB钢连杆的热处理质量检验项目
(续)
5.连杆的常见热处理缺陷和补救措施(表2-19)
表2-19连杆的常见热处理缺陷和补救措施