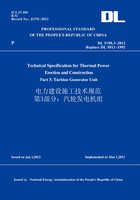
6.2 Electro-hydraulic Regulation and Protection Device
6.2.1 The inspection and assembling of servo valves,solenoid valves and unloading valves of electrohydraulic control system shall comply with the following provisions:
1 For storage of equipment,the package shall be clean,to prevent contamination.
2 During flushing,flushing plates should be used in place of formal valves,and the inside of servomotor shall be flushed by controlling the up and down movement of servomotor with a manual flushing valve.Assemblies shall be installed after flushing and qualification of oil pipes.
3 At time of installation,provisions against dust and water shall be made;the connections and oil inlet and return ports of the hydraulic modules shall be checked and confirmed for correct dimensions and soundness of sealing rings.
4 Surfaces in contact with hydraulic module shall be flat and free of groove or pit,with surface roughness not over ,flatness not greater than 0.02mm/m,and the contact surfaces shall be clean.
5 Fixing bolts shall be homogeneously tightened in a symmetrical pattern,with tightening torque complying with manufacturer requirements.
6.2.2 For servo valves in electro-hydraulic control system,precision filter element shall be fitted upstream the valve before feeding oil,the filtration size of the element shall comply with manufacturer requirements;when there is no requirement from manufacturer,the filtration size should be smaller than 5μm for nozzle baffle type servo valves,smaller than 10μm for a jet pipe type and smaller than 15μm for a direct driven type.
6.2.3 The installation of membrane valves or diaphragm valves in the electro-hydraulic control system shall comply with the following provisions:
1 The valve must be securely fixed and the pipes must not carry the load of the valve.
2 A diaphragm valve shall be installed laterally close to the front bearing housing,but should not be fixed directly on the front bearing housing.
3 The installation of the HP protecting oil pipe in connection with diaphragm valve shall agree with the medium flow direction marked on the valve body.
6.2.4 An air pilot valve should be installed near the front bearing housing and be securely fixed,its vent port must not be directed to people passage,and the length of compressed air pipe connecting with extraction check valve shall be as short as possible.
6.2.5 Parts such as HP governor module,test module and solenoid valve bank arranged separately shall be securely fixed,their installation positions shall comply with manufacturer requirements,and the pipes shall be as short as possible if there is no requirement from manufacturer,to facilitate monitoring and repair.
6.2.6 The joint surfaces of governor module or assembly mounted on front bearing housing shall be flat,and be in close contact with front bearing housing after installation,without leakage from joint surfaces and pipe connections,and the pipe must not exert additional stress on module or assembly.
6.2.7 Mechanical driving mechanisms such as linkages,levers,shafts and handles of the regulation and protection system shall be fixed reliably,operate flexibly at accurate locations,and the operation travel shall comply with manufacturer requirements.
6.2.8 The installation of pilot valves and butterfly valves of the regulation and protection device shall comply with the following provisions:
1 The inside of valve cage shall be clean and free of sundries,and the oil inlet and return ports shall not be blocked.
2 The operation shall be flexible,and the gap between spool,disk and sleeve shall comply with manufacturer requirements.
3 The sealing surfaces of spools and discs shall be smooth and in good contact.
4 The travel of spool shall comply with manufacturer requirements,and the spring shall be able to reset reliably after the acting force has disappeared.
6.2.9 Installation of emergency governor shall comply with the following provisions:
1 Before removing the emergency governor,the position of the nut for fixed spring tightening force shall be recorded,and at the time of replacing,it shall be restored to original position and locked.When there are two emergency governors,their internal parts must not be interchanged.
2 The maximum travel of flying hammer or flying ring shall comply with manufacturer requirements.
3 The radial run out at the shaft end of emergency governor must not exceed 0.05mm.
4 The operation speed of emergency governor shall be tested and adjusted before leaving the factory.
6.2.10 Installation of emergency governor trip lever shall comply with the following provisions:
1 The engaging angle and depth of the trip lever engaging notch shall be correct,the engaging position shall be free of damage,the operation shall be flexible without jamming,the connection shall be free of looseness and the operation travel shall comply with drawing requirements.
2 The gap between trip lever and flying hammer or flying ring after latching shall comply with manufacturer requirements,and should be 0.8mm-1.2mm when there is no requirement from the manufacturer.
6.2.11 Installation of emergency governor oil spray test device shall comply with the following provisions:
1 The oil spray pipes shall be clean and through,the relative position with the emergency governor oil inlet chamber within the maximum expansion differential range of rotor shall meet the test specification,and the gap between nozzles and oil inlet chamber shall comply with specification.
2 The test pull rod shall be able to correctly control the shut-off or opening of the emergency governor valve corresponding to the flying hammer,and the corresponding oil feeding or shut-off of the oil spray pilot valve,and the indication shall be correct.
3 The oil spray test device shall be tested for operation after installation and locating of emergency governor,emergency governor valve and test lever,and shall comply with manufacturer requirements.
4 When emergency governor test device is used directly for oil spray test,the system shall be trial operated and shall comply with the following provisions:
1)The indication of test pilot valve rotation direction and oil circuit switchover shall agree with the numbering of emergency governors.
2)When it is not in oil filling test,the indication pin shall be able to reliably prevent the test pilot valve from rotating or pulling.
6.2.12 Installation of the travel switches and indicators of regulation and protection device shall comply with the following provisions:
1 The contact of a mechanical lever indicator and the contact position of electrical contact travel switch shall comply with requirements on drawings,and after installation,reliable triggering after operation of regulation and protection device shall be confirmed.
2 For an indicator with piston and spring lifted by safety oil,the piston and indicating bar shall operate flexibly without jamming,and the safety oil pipe shall be tight and smooth without leakage.
6.2.13 Installation adjustment of axial displacement and differential expansion protecting device measuring element shall be performed after determining the turbine thrust bearing position and gap,and the setting of measuring elements with respect to zero position of turbine rotor shall comply with manufacturer requirements.
6.2.14 Installation of electromagnetic axial displacement and differential expansion protection device must comply with the following provisions:
1 The axial and radial position and gap of transmitter with the flange on main shaft shall comply with manufacturer requirements,and the internal position shall correspond to external indication.
2 The insulation layer and shield sleeve of transmitter lead-out cable shall be free of damage,and there shall be no leakage at the location it passes the bearing pedestals housing.
3 The installation and adjustment of transmitters shall be done with cooperation from turbine and I&C professional personnel,and after adjustment,the local indicators shall be brought back to zero and the adjustment bars be locked.
6.2.15 The handle of a manual emergency governor shall be provided with a red protection hood,the locating ball shall enable correct locating of pilot valve.
6.2.16 In the installation of electronic protecting devices such as overspeed monitoring protection,vibration monitoring protection and axial displacement monitoring protection,transmitting element shall be adjusted in cooperation with I&C personnel,to ensure correct measuring points and accurate test operation data,and the leads shall be connected to outside reliably.
6.2.17 The hydraulic assemblies,HP fire-resistant oil pump,HP pilot valve and electro-hydraulic conversion valve having adjusted before leaving the factory of the electro-hydraulic control system shall be sealed and stored,and it is not necessary to dismantle and inspect them on-site.
6.2.18 Before installation,the meters and electromagnetic sensing elements of the protecting device shall be checked and calibrated on-spec by I&C professional personnel.