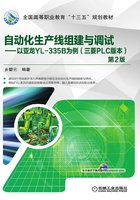
2.2 加工单元的结构和工作过程
加工单元的功能是把待加工工件从物料台移送到加工区域冲压气缸的正下方,完成对工件的冲压加工,然后把加工好的工件重新送回物料台。
加工单元装置侧主要结构组成为:加工台及滑动机构,加工(冲压)机构,电磁阀组,接线端口,底板等。其中,该单元机械结构总成如图2-7所示。

图2-7 加工单元机械结构总成
a)前视图 b)右视图
1.加工台及滑动机构
加工台及滑动机构如图2-8所示。加工台用于固定被加工件,并把工件移到加工(冲压)机构正下方对其进行冲压加工。它主要由气动手指、手爪、加工台伸缩气缸、线性导轨及滑块、磁感应接近开关和漫射型光电式传感器组成。
滑动加工台的工作原理:滑动加工台在系统正常工作后的初始状态为伸缩气缸伸出、加工台气动手指张开,当输送机构把工件送到物料台上,物料检测传感器检测到工件后,PLC控制程序驱动气动手指将工件夹紧→加工台回到加工区域冲压气缸下方→冲压气缸活塞杆向下伸出以冲压工件→完成冲压动作后冲压气缸活塞杆向上缩回→加工台重新伸出→到位后气动手指松开,最终完成工件加工流程,并向系统发出加工完成信号,为下一次工件的到来加工做准备。

图2-8 加工台及滑动机构
在加工台上装有一个漫射型光电接近开关。若加工台上没有工件,则漫射型光电接近开关处于常态;若加工台上有工件,则光电接近开关动作,表明加工台上已有工件。该光电接近开关的输出信号被送到加工单元PLC的输入端,用于判别加工台上是否有工件需要进行加工;当加工过程结束后,加工台伸出到初始位置。同时,PLC通过通信网络,把加工完成信号回馈给系统,以协调控制。
在本实训设备中加工台上安装的漫射型光电接近开关是E3Z-L61型放大器内置型光电接近开关(细小光束型)。
加工台伸出和缩回的极限位置是通过调整伸缩气缸上两个磁性开关位置来定位的。要求缩回位置位于加工冲头正下方;伸出位置应与输送单元的抓取机械手装置配合,确保输送单元的抓取机械手能顺利地把待加工工件放到物料台上。
2.加工(冲压)机构
加工(冲压)机构如图2-9所示。加工(冲压)机构用于对工件进行冲压加工。它主要由冲压气缸、冲压头和安装板等组成。

图2-9 加工(冲压)机构
冲压机构的工作原理:当工件到达冲压位置即伸缩气缸活塞杆缩回到位时,冲压气缸伸出对工件进行加工,完成加工动作后冲压气缸缩回,为下一次冲压做准备。
冲压头被安装在冲压气缸头部,根据工件的加工要求对工件进行冲压加工。安装板用于安装冲压气缸,对冲压气缸进行固定。
2.2.1 加工单元PLC的I/O接线
加工单元PLC的I/O接线如图2-10所示。

图2-10 加工单元PLC的I/O接线图
a)Fx2N-32MR的I/O接线图

图2-10 加工单元PLC的I/O接线图(续)
b)Fx3U-32M的I/O接线图
2.2.2 加工单元气动控制回路工作原理
加工单元的气动控制元件均采用二位五通单电控电磁换向阀,各电磁阀均带有手动换向和加锁钮。它们被集中安装成阀组而固定在冲压支架后面。
气动控制回路的工作原理如图2-11所示。3B1和3B2为安装在冲压气缸两个极限工作位置的磁感应接近开关,2B1和2B2为安装在加工台伸缩气缸的两个极限工作位置的磁感应接近开关,1B1和1B2为安装在工件夹紧气缸工作位置的磁感应接近开关。3Y1、2Y1和1Y1分别为控制冲压气缸、加工台伸缩气缸和工件夹紧气缸的电磁阀的电磁控制端。

图2-11 加工单元气动控制回路工作原理图
2.2.3 加工单元调试与运行
1.工作任务
本节只考虑加工单元作为独立设备运行时的情况,加工单元的按钮和指示灯模块上的工作方式选择开关应置于“单站方式”位置。其具体的控制要求如下。
1)初始状态:设备通电和气源接通后,滑动加工台伸缩气缸处于伸出位置,加工台气动手指处于松开的状态,冲压气缸处于缩回位置,急停按钮没有被按下。
若设备处在上述初始状态,则“正常工作”指示灯HL1常亮,表示设备准备好。否则,该指示灯以1Hz的频率闪烁。
2)若设备已准备好,则按下启动按钮,设备启动,“设备运行”指示灯HL2常亮。当待加工工件被送到加工台上并检出后,设备执行将工件夹紧的动作,然后将其送往加工区域冲压,完成冲压动作后返回待料位置。如果没有停止信号输入,当再有待加工工件被送到加工台上时,加工单元又开始下一周期工作。
3)在工作过程中,若按下停止按钮,则加工单元在完成本周期的动作后停止工作。指示灯HL2熄灭。
本节要求完成的任务总结如下。
1)规划PLC的I/O分配及接线端子分配。
2)进行系统安装接线和气路连接。
3)编制PLC程序。
4)进行调试与运行。
2.编写和调试PLC控制程序
加工单元工作流程与供料单元类似,也是PLC通电后应首先进入初始状态检查阶段,确认系统已经准备就绪后,才允许接收启动信号投入运行。但加工单元工作任务中增加了急停功能。为了使急停发生后系统停止工作的同时能进行状态保持,以便急停复位后能从急停前的断点开始继续运行,可以采用两种方法实现,一是用条件跳转(CJ)指令实现,另一种方法是用主控指令实现。这里暂且只讨论用条件跳转(CJ)指令实现的方法。
用条件跳转指令实现急停信号处理的程序梯形图如图2-12所示。图中,当急停按钮被按下时,跳转指令执行条件满足,程序跳转到指令所指定的指针标号P0处继续执行。安排在跳转指令后面的步进顺序控制程序段被跳转而不再执行。

图2-12 急停信号处理的程序梯形图
由于执行条件跳转指令后,被跳转部分程序将不再被扫描,这意味着,跳转前的输出状态(执行结果)将被保留,步进顺序控制程序段的状态将被保持,直到急停按钮复位后加工单元又能继续工作。但必须注意的是,如果急停恰好发生在S22步,正值冲压头压下,则程序跳转后,压下状态将会被保持下来,因此需要在FEND指令与END指令之间加上复位冲压电磁阀的程序段。
当急停按钮未被按下时,程序按顺序执行,直至遇到主程序结束指令FEND为止。
3.调试与运行
1)调整气动部分,检查气路是否正确,气压是否合理,气缸的动作速度是否合理。
2)检查磁性开关的安装位置是否到位,磁性开关工作是否正常。
3)检查I/O接线是否正确。
4)检查光电式传感器安装是否合理,灵敏度是否合适,保证检测的可靠性。
5)放入工件,运行程序并观察加工单元动作是否满足任务要求。
6)调试各种可能出现的情况,确保任何情况下加入工件,系统都能可靠工作。
7)优化程序。
问题与思考
● 总结气动连线、传感器接线、I/O接线的检查及故障排除方法。
● 如果在加工过程中出现意外情况应如何处理。
● 如果采用网络控制应如何实现?
● 加工单元各种可能会出现的问题是什么?